3.4 Rugosidad
3.4. Rugosidad
3.4.10 Simbología relacionada con rugosidad
3.4.2 Características que definen el estado de la superficie
3.4.3 Análisis de una superficie
3.4.4 sistemas que existen para medir la rugosidad
3.4.5 Elementos del signo del estado de la superficie
3.4.6 Rugosidad obtenida por diferentes procesos y sus aplicaciones
3.4.7 Promedio de rugosidad por diferentes procesos
3.4. Rugosidad

Superficie real: Superficie que limita el cuerpo y lo separa del medio que lo separa.
Superficie geométrica: Superficie ideal cuya forma está especificada por el dibujo y/o todo documento técnico.
Superficie de referencia: Superficie a partir de la cual se determinan los parámetros de rugosidad. Tiene la forma de la superficie geométrica. Se puede calcular por el método de mínimos cuadrados.
Perfil real: es la intersección de la superficie real con un plano normal.

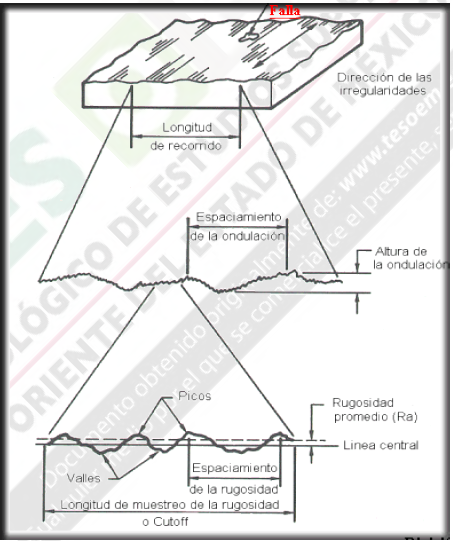
La rugosidad de la superficie se determina considerando la longitud de onda del radar y el ángulo de incidencia. Una superficie aparecerá ser lisa si sus variaciones de la altura son más pequeñas que 1/8 de la longitud de onda del radar.
En términos del uso de una determinada longitud de onda, una superficie aparece más lisa mientras la longitud de onda y el ángulo de incidencia aumenta.
En imágenes generadas por radares, las superficies ásperas aparecerán más brillantes que superficies más lisas del mismo material. La aspereza superficial influencia la reflectividad de la energía de la microonda.
Las superficies lisas horizontales que reflejan casi toda la energía de la incidencia lejos del radar se llaman los reflectores especulares, ejemplos de estas superficies, son el agua tranquila o caminos pavimentados que aparecen oscuras en las imágenes de radar. En cambio las superficies ásperas dispersan la energía de la microonda incidente en muchas direcciones, esto se conoce como reflexión difusa. Las superficies vegetales causan reflexión difusa y generan imágenes con un tono más brillante.

Es importante diferenciar entre la rugosidad de una superficie y la ondulación
de la misma. Para evitar que la ondulación interfiera en la medición de
la rugosidad, suelen utilizarse filtros electrónicos (llamados
Cut-off). Los errores de forma de la superficie tampoco son tenidos en
cuenta. Para saber más sobre los filtros o Cut-off visita la Referencia 1 y 13 que se encuentra al final del artículo.
Tanto la rugosidad como la ondulación se combinan para dar el perfil real de la superficie. A
anto la rugosidad como la ondulación se combinan para dar el perfil real de la superficie. A continuación una imagen para entenderlo mejor:


Gráficamente la rugosidad Ra sería así:

Como notarás, al ser un “Promedio” no tiene en cuenta la presencia de
picos muy altos, o valles muy hondos, algo que puede ser indeseado
dependiendo de la funcionalidad de la pieza. Para saber más sobre
los tipos de rugosidades en superficies visita las Referencias 2 y 3,
que se encuentra al final de este artículo.

3.4.10 Simbología relacionada con rugosidad

Es importante notar que el valor de la rugosidad no se indica más
como solía hacerse, es decir, colocando el número sobre “el triángulo”.
En la siguiente imagen se muestra la forma correcta de indicar los
distintos aspectos de la rugosidad mediante simbología normalizada por
ISO:

Seguramente encontrarás en muchos textos que la rugosidad se indica
en el lugar donde esta la “X” entre paréntesis, pero desde hace unos
años se coloca en donde esta la referencia “a”. Obviamente, estos
cambios siempre se prestan a confusión, y lo más importante es estar
“de acuerdo” con la persona que va a “leer” esos planos.
Para saber más visita la sección 1 de la Referencia 2, que se encuentra al final de este artículo.


Obviamente, esto no es aplicable el 100% de las situaciones. Debemos
prestar mucha atención a nuestro criterio de diseño y nuestra “intuición
profesional”, al menos para tener una guía o referencia más a la hora
de definir estos y otros parámetros.
Algo poco frecuente, pero que en algunas ocasiones es necesario indicar, es la dirección de las “marcas de mecanizado”. A continuación los tipos mas comunes y el símbolo normalizado que se utiliza para indicarlo:

3.4.2 Características que definen el estado de la superficie
Características
Promedio de rugosidad: El valor promedio de rugosidad en µm es el valor promedio aritmético de los valores absolutos de las distancias del perfil de rugosidad de la línea intermedia de la longitud de medición. El valor promedio de rugosidad es idéntico a la altura de un rectángulo donde su longitud es igual a la longitud total lm y esto a su vez es idéntico con la superficie de la suma que existe entre el perfil de rugosidad y la línea intermedia. Rz: Promedio de la profundidad de la rugosidad en µm (promedio aritmético de cinco profundidades singulares consecutivas en la longitud de medición). Los rugosímetros sirven para detectar de forma rápida las profundidades de la rugosidad en las superficies de materiales. Los rugosímetros le indican en µm la profundidad de la rugosidad Rz y el promedio de rugosidad Ra. Tenemos disponibles equipos con un máximo de trece parámetros de medida. Son aplicables las siguientes normativas en la comprobación de rugosidad en las superficies delas piezas de trabajo: DIN 4762, DIN 4768, DIN 4771, DIN 4775. La rugosidad alcanzable de las superficies las puede ver en DIN 4766±1. Los rugosímetros se envían calibrados (pero sin certificado). Opcionalmente puede obtener para los rugosímetros una calibración de laboratorio, incluido el certificado ISO. Así podrá integrar sus medidores en su control de calidad ISO y calibrarlos anualmente (a través de PCE o cualquier laboratorio acreditado).
Rugosidad obtenida: El costo de una superficie maquinada crece cuando se desea un mejor acabado superficial, razón por la cual el diseñador deberá indicar claramente cual es el valor de rugosidad deseado, ya que no siempre un buen acabado superficial redundará en un mejor funcionamiento de la pieza, como sucede cuando desea lubricación eficiente y por tanto una capa de aceite debe mantenerse sobre la superficie.
En el pasado el mejor método práctico para decidir si un acabado superficial cumplía con los requerimientos era comparado visualmente y mediante el tacto contra muestras con diferentes acabados superficiales .Este método no debe confundirse con los patrones de rugosidad que actualmente se usan en la calibración de rugosimetros.

Tipos de medición de rugosidad
Los sistemas más utilizados son el de rugosidad Ra, rugosidad Rx, rugosidad Ry y rugosidad Rz. Los más usuales son Ra. Rz, Ry. Ra
Los valores absolutos de los alejamientos del perfil desde la línea central.
La altura de un rectángulo de longitud lm, cuya área, es igual a la suma de las áreas delimitadas por el perfil de rugosidad y la línea central Rz.
Promedio de las alturas de pico a valles. La diferencia entre el promedio de las alturas delos cinco picos más altos y la altura promedio de los cinco valles más profundos Ry.
La máxima altura del perfil. La distancia entre las líneas del perfil de picos y valles.
3.4.4 Sistemas que existen para medir la rugosidad
Medida de rugosidad:
Comparadores visotáctiles. Elementos para evaluar el acabado superficial de piezas por comparación visual y táctil con superficies de diferentes acabados obtenidas por el mismo proceso de fabricación.
Rugosímetro de palpador mecánico:
Instrumento para la medida de la calidad superficial pasado en la amplificación eléctrica dela señal generada por un palpador que traduce las irregularidades del perfil de la sección dela pieza. Sus elementos principales son el palpador, el mecanismo de soporte y arrastre de éste, el amplificador electrónico, un calculador y un registrador.
Rugosímetro: Palpador inductivo. El desplazamiento de la aguja al describir las irregularidades del perfil modifica la longitud del entrehierro del circuito magnético, y con ello el flujo de campo magnético que lo atraviesa, generando una señal eléctrica.
Rugosímetro: Palpador capacitivo. El desplazamiento vertical del palpador aproxima las dos láminas de un condensador, modificando su capacidad y con ella la señal eléctrica.
Rugosímetro: Palpador piezoeléctrico: El desplazamiento de la aguja del palpador de forma elásticamente un material piezoeléctrico, que responde a dicha deformación generando una señal eléctrica.
Rugosímetro: Patín mecánico: El patín describirá las ondulaciones de la superficie mientras la aguja recorra los picos y valles del perfil. Así se separan mecánicamente ondulación y rugosidad que son simplemente desviaciones respecto de la superficie geométrica con distinta longitud de onda.
Rugosímetro: Filtrado eléctrico: La señal eléctrica procedente del palpador puede pasar a un filtro para eliminar las ondulaciones, esto es, disminuir la amplitud de sus componentes a partir de una longitud de onda ᵞ´, (longitud de onda de corte).
En el SI 1µm = 0,001mm
En el sistema anglosajón 1µinch = 0,000001 inch (pulgada)
El principio de funcionamiento de un Rugosímetro es (explicado en forma sencilla) el siguiente:

Luego esa señal es procesada por un circuito electrónico en el cual
se han definido previamente parámetros necesarios, como por ejemplo el
cutoff que hablamos anteriormente. La longitud de muestreo es un factor
importante a la hora de configurar nuestro rugosímetro. El flujo de procesamiento de los datos captados por el palpador es aproximadamente el siguiente:

3.4.5 Elementos del signo del estado de la superficie
3.4.6 Rugosidad obtenida por diferentes procesos y sus aplicaciones
3.4.10 Simbología relacionada con rugosidad
3.4.2 Características que definen el estado de la superficie
3.4.3 Análisis de una superficie
3.4.4 sistemas que existen para medir la rugosidad
3.4.5 Elementos del signo del estado de la superficie
3.4.6 Rugosidad obtenida por diferentes procesos y sus aplicaciones
3.4.7 Promedio de rugosidad por diferentes procesos
3.4. Rugosidad
- La rugosidad superficial es el conjunto de irregularidades de la superficie real, definidas convencionalmente en una sección donde los errores de forma y las ondulaciones han sido eliminados.

Superficie real: Superficie que limita el cuerpo y lo separa del medio que lo separa.
Superficie geométrica: Superficie ideal cuya forma está especificada por el dibujo y/o todo documento técnico.
Superficie de referencia: Superficie a partir de la cual se determinan los parámetros de rugosidad. Tiene la forma de la superficie geométrica. Se puede calcular por el método de mínimos cuadrados.
Perfil real: es la intersección de la superficie real con un plano normal.

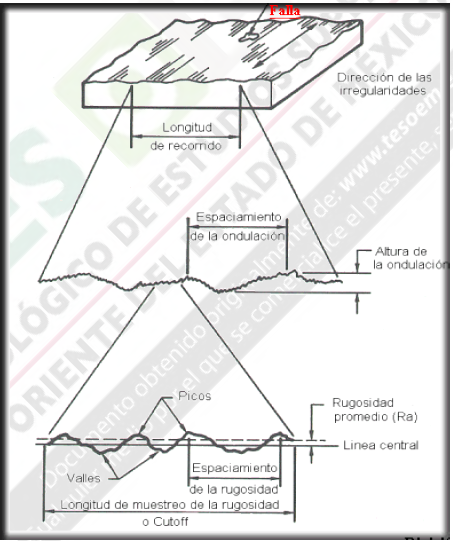
La rugosidad de la superficie se determina considerando la longitud de onda del radar y el ángulo de incidencia. Una superficie aparecerá ser lisa si sus variaciones de la altura son más pequeñas que 1/8 de la longitud de onda del radar.
En términos del uso de una determinada longitud de onda, una superficie aparece más lisa mientras la longitud de onda y el ángulo de incidencia aumenta.
En imágenes generadas por radares, las superficies ásperas aparecerán más brillantes que superficies más lisas del mismo material. La aspereza superficial influencia la reflectividad de la energía de la microonda.
Las superficies lisas horizontales que reflejan casi toda la energía de la incidencia lejos del radar se llaman los reflectores especulares, ejemplos de estas superficies, son el agua tranquila o caminos pavimentados que aparecen oscuras en las imágenes de radar. En cambio las superficies ásperas dispersan la energía de la microonda incidente en muchas direcciones, esto se conoce como reflexión difusa. Las superficies vegetales causan reflexión difusa y generan imágenes con un tono más brillante.
Conceptos Básicos
Generalmente cuando hablamos de rugosidad nos referimos a las irregularidades encontradas sobre un plano que intersecta perpendicularmente a la superficie de la pieza. La siguiente imagen lo demuestra:Tanto la rugosidad como la ondulación se combinan para dar el perfil real de la superficie. A
anto la rugosidad como la ondulación se combinan para dar el perfil real de la superficie. A continuación una imagen para entenderlo mejor:
Tipos de rugosidades
Si bien hay varios tipos de rugosidad superficial, la más utilizada en todo el mundo es la Desviación media aritmética del perfil (Ra), cuya fórmula se encuentra en la imagen inferior:Normas de Rugosidad Superficial
Si bien la norma que utilicemos para indicar la rugosidad dependerá del país en donde residamos, o para el cual estemos trabajando, la unificación mundial avanza, y es por ello que las normas ISO (International Standard Organization) van ganando terreno poco a poco. A continuación dejo una imagen sobre las normas ISO que tratan de rugosidad superficial:3.4.10 Simbología relacionada con rugosidad
Indicación de Rugosidad en planos – Símbolos y acotaciones correctas
Ya vimos cuales son las normas ISO sobre rugosidad que aplican. Según la ISO 1302, los símbolos correctos para indicar la rugosidad de una superficie son:Para saber más visita la sección 1 de la Referencia 2, que se encuentra al final de este artículo.
Rugosidades obtenidas según la técnica de mecanizado
No hace falta aclarar que dependiendo del mecanizado que se le va a efectuar a la pieza, obtendremos una rugosidad aceptable para eso operación. Por ejemplo, no podemos esperar una calidad superficial igual al lapeado en un torno (algo bastante obvio). La siguiente imagen da una idea a las rugosidades que seguramente obtendremos por cada tipo de mecanizado:Relación entre la tolerancia y la rugosidad
De nada sirve tener una rugosidad similar a la obtenida con un lapeado, por ejemplo, y una tolerancia dimansional IT14. Genralmente (para no decir “siempre”) las rugosidades superficiales de una pieza tienen relación estrecha con la tolerancia dimensional de la misma. La siguiente imagen da una idea de los que estamos hablando:Algo poco frecuente, pero que en algunas ocasiones es necesario indicar, es la dirección de las “marcas de mecanizado”. A continuación los tipos mas comunes y el símbolo normalizado que se utiliza para indicarlo:
3.4.2 Características que definen el estado de la superficie
Características
Promedio de rugosidad: El valor promedio de rugosidad en µm es el valor promedio aritmético de los valores absolutos de las distancias del perfil de rugosidad de la línea intermedia de la longitud de medición. El valor promedio de rugosidad es idéntico a la altura de un rectángulo donde su longitud es igual a la longitud total lm y esto a su vez es idéntico con la superficie de la suma que existe entre el perfil de rugosidad y la línea intermedia. Rz: Promedio de la profundidad de la rugosidad en µm (promedio aritmético de cinco profundidades singulares consecutivas en la longitud de medición). Los rugosímetros sirven para detectar de forma rápida las profundidades de la rugosidad en las superficies de materiales. Los rugosímetros le indican en µm la profundidad de la rugosidad Rz y el promedio de rugosidad Ra. Tenemos disponibles equipos con un máximo de trece parámetros de medida. Son aplicables las siguientes normativas en la comprobación de rugosidad en las superficies delas piezas de trabajo: DIN 4762, DIN 4768, DIN 4771, DIN 4775. La rugosidad alcanzable de las superficies las puede ver en DIN 4766±1. Los rugosímetros se envían calibrados (pero sin certificado). Opcionalmente puede obtener para los rugosímetros una calibración de laboratorio, incluido el certificado ISO. Así podrá integrar sus medidores en su control de calidad ISO y calibrarlos anualmente (a través de PCE o cualquier laboratorio acreditado).
Rugosidad obtenida: El costo de una superficie maquinada crece cuando se desea un mejor acabado superficial, razón por la cual el diseñador deberá indicar claramente cual es el valor de rugosidad deseado, ya que no siempre un buen acabado superficial redundará en un mejor funcionamiento de la pieza, como sucede cuando desea lubricación eficiente y por tanto una capa de aceite debe mantenerse sobre la superficie.
En el pasado el mejor método práctico para decidir si un acabado superficial cumplía con los requerimientos era comparado visualmente y mediante el tacto contra muestras con diferentes acabados superficiales .Este método no debe confundirse con los patrones de rugosidad que actualmente se usan en la calibración de rugosimetros.
Tipos de medición de rugosidad
Los sistemas más utilizados son el de rugosidad Ra, rugosidad Rx, rugosidad Ry y rugosidad Rz. Los más usuales son Ra. Rz, Ry. Ra
Los valores absolutos de los alejamientos del perfil desde la línea central.
La altura de un rectángulo de longitud lm, cuya área, es igual a la suma de las áreas delimitadas por el perfil de rugosidad y la línea central Rz.
Promedio de las alturas de pico a valles. La diferencia entre el promedio de las alturas delos cinco picos más altos y la altura promedio de los cinco valles más profundos Ry.
La máxima altura del perfil. La distancia entre las líneas del perfil de picos y valles.
3.4.4 Sistemas que existen para medir la rugosidad
Medida de rugosidad:
Comparadores visotáctiles. Elementos para evaluar el acabado superficial de piezas por comparación visual y táctil con superficies de diferentes acabados obtenidas por el mismo proceso de fabricación.
Rugosímetro de palpador mecánico:
Instrumento para la medida de la calidad superficial pasado en la amplificación eléctrica dela señal generada por un palpador que traduce las irregularidades del perfil de la sección dela pieza. Sus elementos principales son el palpador, el mecanismo de soporte y arrastre de éste, el amplificador electrónico, un calculador y un registrador.
Rugosímetro: Palpador inductivo. El desplazamiento de la aguja al describir las irregularidades del perfil modifica la longitud del entrehierro del circuito magnético, y con ello el flujo de campo magnético que lo atraviesa, generando una señal eléctrica.
Rugosímetro: Palpador capacitivo. El desplazamiento vertical del palpador aproxima las dos láminas de un condensador, modificando su capacidad y con ella la señal eléctrica.
Rugosímetro: Palpador piezoeléctrico: El desplazamiento de la aguja del palpador de forma elásticamente un material piezoeléctrico, que responde a dicha deformación generando una señal eléctrica.
Rugosímetro: Patín mecánico: El patín describirá las ondulaciones de la superficie mientras la aguja recorra los picos y valles del perfil. Así se separan mecánicamente ondulación y rugosidad que son simplemente desviaciones respecto de la superficie geométrica con distinta longitud de onda.
Rugosímetro: Filtrado eléctrico: La señal eléctrica procedente del palpador puede pasar a un filtro para eliminar las ondulaciones, esto es, disminuir la amplitud de sus componentes a partir de una longitud de onda ᵞ´, (longitud de onda de corte).
Rugosímetros y medición de la rugosidad
La medida universal de medición es el micrómetro (µm), aunque también suele utilizarse la micropulgada (µinch):En el SI 1µm = 0,001mm
En el sistema anglosajón 1µinch = 0,000001 inch (pulgada)
El principio de funcionamiento de un Rugosímetro es (explicado en forma sencilla) el siguiente:
3.4.5 Elementos del signo del estado de la superficie
3.4.6 Rugosidad obtenida por diferentes procesos y sus aplicaciones
Procesos de fabricación
Procesos para mecanizado del material
La fabricación de piezas mediante arranque de viruta o material se consigue a partir del mecanizado de su superficie, lo que puede realizarse por varios procedimientos, entre ellos:
A) Fresado.
Arranque de viruta mediante la acción de una herramienta con dientes de filos cortantes, denominada fresa, que gira alrededor de su eje, pudiendo actual tangencial o frontalmente respecto a la superficie mecanizada (Figura 1.14).
Fig. 1.14 Fresado tangencial y frontal. Fuente: Hidalgo de Caviedes, 1975.
B) Torneado.
Se denomina así al procedimiento de fabricación para el que se emplea la máquina–herramienta considerada como fundamental, el torno. Con ella se pueden realizar múltiples operaciones, aunque la más importante es el torneado o fabricación de piezas de revolución (Figura 1.15).
Fig. 1.15 Esquema de un torno. Fuente: Hidalgo de Caviedes, 1975.
C) Taladrado.
Consiste en la perforación de una pieza, parcial (taladro ciego) o totalmente (taladro pasante), mediante una herramienta llamada broca. La broca gira alrededor de su eje de revolución a la vez que se desplaza en la dirección del mismo.
D) Aserrado.
Procedimiento de fabricación que consta de una herramienta de acero denominada sierra, dotada de un movimiento alternativo longitudinal, con la cual se consigue cortar chapas y planchas. También se puede realizar este tipo de cortes con un soplete oxiacetilénico.
Por otra parte, los procedimientos de fabricación sin arranque de viruta tienen la particularidad de que moldean o forjan el material sin arrancar parte del mismo. Entre estos procedimientos de fabricación podemos destacar:
A) Fundición.
Consiste en rellenar un molde o modelo negativo de la pieza a fabricar con metal fundido. Una vez enfriado el metal se procede al desmoldeo para obtener la pieza deseada. Según el tipo de molde utilizado diferenciamos el moldeo en arena, moldeo en molde metálico o coquilla (fundición mediante inyección de metal fundido a presiones de 25–50 atmósferas), y moldeo a la cera o resina perdida.
B) Forja.
Consiste en la conformación de la pieza mediante golpes o prensado, calentándola previamente para facilitar la operación. Dentro de la forja podemos diferenciar:
— Forja manual o libre. Conformación de la pieza a través de mazo y yunque.
— Forja en estampa. Consiste en utilizar una prensa que consta de estampa y contra estampa. La estampa o matriz, que actúa como yunque, contiene el vaciado correspondiente a la forma de la pieza, mientras la contra estampa o martillete, que actúa como mazo, golpea la estampa, prensando el material previamente calentado para mejorar su fluidez, de forma que éste rellena el vaciado de la matriz.
Fig. 1.16 Esquema de máquina laminadora. Fuente: Hidalgo de Caviedes, 1975.
C) Laminado.
Se emplea en la obtención de perfiles laminados de gran longitud en relación a su sección transversal.
Por ejemplo, es muy utilizado en la fabricación de perfiles resistentes de construcciones agroindustriales metálicas (perfiles IPN, UPN, etc.). La laminadora es una máquina que consta de dos árboles horizontales y paralelos en los que se acoplan sendos cilindros simétricos que dejan una zona libre con la forma requerida por el perfil. Generalmente el proceso precisa de varias pasadas por diferentes trenes de laminado, de forma que se logre una transición gradual de la pieza en basto al perfil de diseño.
D) Extrusionado.
Operación consistente en obligar a pasar por un orificio de forma predeterminada a un material o metal en estado fluido.
La indicación en los dibujos técnicos de la rugosidad superficial de diseño se lleva a cabo mediante la asignación del valor numérico de máxima rugosidad tolerada (Figura 9.8). Si no se disponen unidades se supone que dicho valor se expresa en micrómetros.
Procesos de fabricación especiales
En algunas ocasiones es necesario especificar algunas características o exigencias adicionales para la ejecución de una determinada superficie. Estas características deben consignarse sobre un trazo horizontal dispuesto a partir del trazo más largo del símbolo básico
a) Procesos de fabricación o acabado superficial especiales.
- Rectificado. Operación cuyo objetivo es conseguir un excelente acabado superficial. Aunque puede realizarse con fresa o torno, el mejor grado de calidad se consigue con la herramienta denominada muela, constituida por granos de material abrasivo cementados con una substancia cerámica.
- Bruñido. Su objeto es obtener una superficie con una rugosidad muy pequeña. Generalmente se emplea en el acabado de piezas de precisión, realizando el afinado mediante una muela recubierta de piel.
- Rasqueteado. Es una operación realizada de forma manual con una herramienta llamada rasquete, que sirve para alisar y mejorar la calidad de dos superficies funcionales que van a estar en contacto.
- Moleteado. Operación consistente en tallar sobre una parte de una pieza una serie de estrías que la hacen más rugosa. Se usa para asegurar el agarre del mango o empuñadura de una pieza o herramienta.
El moleteado se consigue con una herramienta denominada moleta, de material más duro que la pieza a grabar, que se presiona sobre la zona a moletear. La forma del moleteado puede ser recta (paralela a las generatrices del cilindro; figura 1.17), oblicua (líneas helicoidales) o cruzada (líneas helicoidales de paso contrario; figura 1.17).
Fig. 1.17. Aplicación de moleteados cruzados y rectos. Fuente: Hidalgo de Caviedes, 1975.
- Limado. Rebaje de una superficie practicado con una herramienta llamada lima.
- Escariado. Operación realizada con un escariador cuyo objetivo es la mejora de la calidad superficial de taladros cilíndricos.
b) Tratamientos térmicos.
Son operaciones de acabado superficial cuyo objetivo primordial es generalmente aumentar la dureza del material y resistencia al desgaste, facilitar su mecanizado y/o conferirle algunas propiedades específicas.
- Templado. Fuerte calentamiento de una pieza de acero, seguido de un enfriamiento. La temperatura alcanzada y la rapidez del enfriamiento dependen de la calidad del acero y de la dureza perseguida.
- Revenido. Tratamiento térmico posterior al templado que intenta limitar la presencia de grietas debidas al enfriamiento rápido. Suele dar una mayor tenacidad al acero. Las operaciones de templado y revenido son práctica habitual en la fabricación de herramientas de acero.
- Recocido. Consiste en elevar la temperatura del hierro o del acero para continuar con un enfriamiento lento. Facilita el posterior mecanizado de la pieza.
- Cementado. Operación compleja basada en un tratamiento térmico del hierro o del acero para añadirle alguna substancia que mejore básicamente su dureza. Un ejemplo podría ser la aplicación de un cemento carburante.
c) Recubrimientos o revestimientos.
Se emplean para proteger al material de la pieza de agentes externos agresivos, mejorando su resistencia al desgaste y corrosión. También pueden tener como objetivo la capacitación de la pieza para ciertas funciones específicas, por ejemplo la de aislamiento eléctrico. Según el material con el que se recubra la superficie podemos hablar de niquelado (Ni), cromado (Cr), estañado (Sn), etc. En estos casos la operación de revestimiento consiste en un galvanizado mediante baño electrolítico. El esmaltado, cuyo objetivo fundamental es la protección y mejora de la estética de una pieza, se consigue mediante la aplicación de una capa de esmalte y su posterior vitrificación en horno.
Moleteado
El moleteado es una operación de realizar sobre la superficie exterior unas estrías que impidan el deslizamiento, se realiza sin arranque de viruta con la ayuda de unos rodillos, llamados moletas, aplicadas tangencialmente a gran presión.
La norma DIN 82 especifica diferentes formas de moleteado, en función de la disposición del relieve y a la dirección de las estrías del moleteado. Cada una de estas formas, con sus variantes respectivas, recibe un símbolo literal (ver figura 1.18).
Fig. 1.18
La indicación de un moleteado se indica con el signo general de acabado superficial, añadiendo la especificación de sus características sobre un trazo horizontal, la cuál incluirá: forma, paso, ángulo y norma.
Los moleteados se representan utilizando el patrón de sombreado correspondiente con línea continua de trazo fino. Si la superficie moleteada se refiere a una parte limitada de la pieza, ésta deberá acotarse.
Diámetro nominal es el indicado en el plano y corresponde con la dimensión resultante después de realizar el moleteado.
El paso es la distancia entre los vértices de dos relieves consecutivos. Los pasos normalizados son: 0.5-0.6-0.8-1-1.2-1.6 mm.
Angulo del perfil es el ángulo que forman los flancos de un relieve. Los valores normalizados son 90° y 105°
Fig. 1.19
Algunas aplicaciones de los estados superficiales
3.4.7 Promedio de rugosidad por diferentes procesos
Sabrías decirme cual es el promedio Rz de los casquillos de una cadena de bicicleta u otros datos si los tuvieras de la misma. Ni que decir tiene que no todas las cadenas son iguales pero igual tienes una idea mayor a la mia.
ResponderEliminar